Injection Mold Making: The Art of Precision Manufacturing
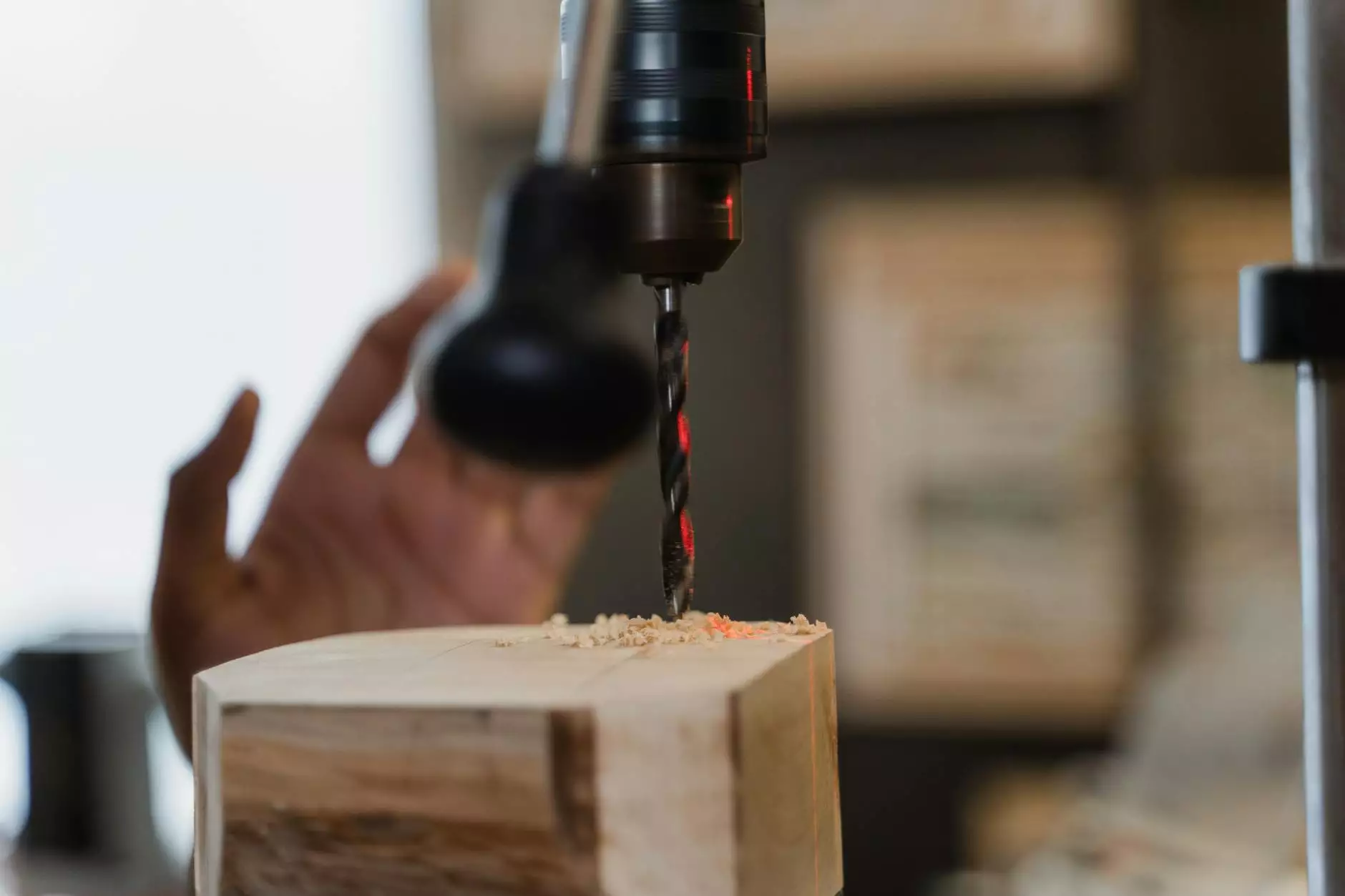
Welcome to QuickParts.com, your one-stop solution for all your metal fabrication and 3D printing needs. Our team of highly skilled professionals specializes in precision manufacturing, with a particular focus on injection mold making. In this comprehensive article, we will delve into the intricacies of injection mold making, exploring the manufacturing process, its applications, and the benefits it offers. Get ready to dive into a world of precision engineering!
The Basics of Injection Mold Making
Injection mold making is a fundamental process in the manufacturing industry, enabling the production of complex and precise components with ease. It involves the creation of custom molds that are used to shape molten materials, typically plastics, into specific forms. These molds are meticulously designed to ensure accuracy, durability, and efficiency in the manufacturing process.
The Injection Mold Making Process
The injection mold making process consists of various stages that require technical expertise and attention to detail. Here's an overview of the key steps involved:
- Design: In this initial stage, skilled engineers develop the design and specifications for the injection mold. They consider factors such as part geometry, material selection, and production volume to create a mold that meets the client's requirements.
- Material Selection: Choosing the right material is crucial for successful injection mold making. Factors such as strength, flexibility, and heat resistance are taken into account to determine the optimal material for the mold.
- Tooling: Once the design and material selection are finalized, the mold-making process moves on to tooling. Skilled technicians use advanced machinery and techniques to craft precision molds, ensuring adherence to tight tolerances.
- Injection: When the mold is ready, the injection process begins. Molten material is injected into the mold, filling it and taking its intended shape. Pressure, temperature, and other parameters are carefully controlled to achieve the desired results.
- Cooling and Ejection: After the material solidifies, the mold is cooled to ensure proper setting. The solidified component is then ejected from the mold, ready for further processing or assembly.
- Finishing: Depending on the final product requirements, additional finishing processes may be involved, such as trimming, polishing, or surface treatment. These steps enhance the overall quality and aesthetics of the components.
Applications of Injection Mold Making
Injection mold making finds extensive applications across various industries. Its versatility, coupled with the ability to produce intricate and accurate components, makes it a preferred manufacturing method for many. Here are some common applications:
Automotive Industry
The automotive industry heavily relies on injection mold making for the production of components such as interior trims, bumpers, dashboards, and precision parts for engines and electrical systems. With the increasing demand for lightweight vehicles and improved fuel efficiency, injection mold making plays a crucial role in creating complex lightweight structures.
Consumer Electronics
From smartphones to home appliances, injection mold making is vital for the production of countless consumer electronic devices. The process enables the manufacturing of intricate casings, buttons, connectors, and other components with high precision and durability.
Medical and Healthcare
The medical and healthcare industry relies on injection mold making for the production of medical devices, surgical instruments, drug delivery systems, and various other critical components. The process ensures the production of sterile, high-quality, and reliable products that meet stringent industry standards.
The Benefits of Injection Mold Making
Injection mold making offers several advantages over alternative manufacturing methods. Let's explore some key benefits:
Precision and Accuracy
Injection mold making allows for the production of highly accurate and precise components, ensuring consistent quality and dimensional accuracy. With the ability to create intricate geometries, it meets the demands of industries where precision is paramount.
Cost-Effectiveness and Efficiency
While injection mold making may involve upfront costs related to mold design and tooling, it offers remarkable cost-effectiveness in large-scale production runs. The process enables high-volume production with reduced labor costs, resulting in savings in the long run. Moreover, the automated nature of injection molding ensures efficient production cycles.
Versatility and Design Freedom
Injection mold making allows for the creation of complex shapes and intricate designs, providing manufacturers with unparalleled design freedom. From undercuts and thin walls to multi-cavity molds, this process opens up a world of possibilities for innovative product development.
Material Selection
Injection mold making supports a wide range of materials, including various thermoplastics, elastomers, and even some metals. This flexibility enables manufacturers to choose the most suitable material for their specific application, considering factors such as strength, rigidity, chemical resistance, and more.
Choose QuickParts.com for Your Injection Mold Making Needs
When it comes to precision manufacturing, QuickParts.com is your trusted partner. As industry leaders in metal fabrication and 3D printing, we have honed our expertise in injection mold making, delivering top-quality products to our clients worldwide.
With our state-of-the-art facilities, cutting-edge technology, and a dedicated team of professionals, we ensure that your project receives the attention it deserves. Whether you require small-scale production or large-volume manufacturing, we have the capabilities to meet your needs.
Contact QuickParts.com today to learn more about our injection mold making services and how we can assist you in bringing your ideas to life. Experience the art of precision manufacturing with our innovative solutions and unmatched quality.