The Essential Role of Production SLA in Business Success
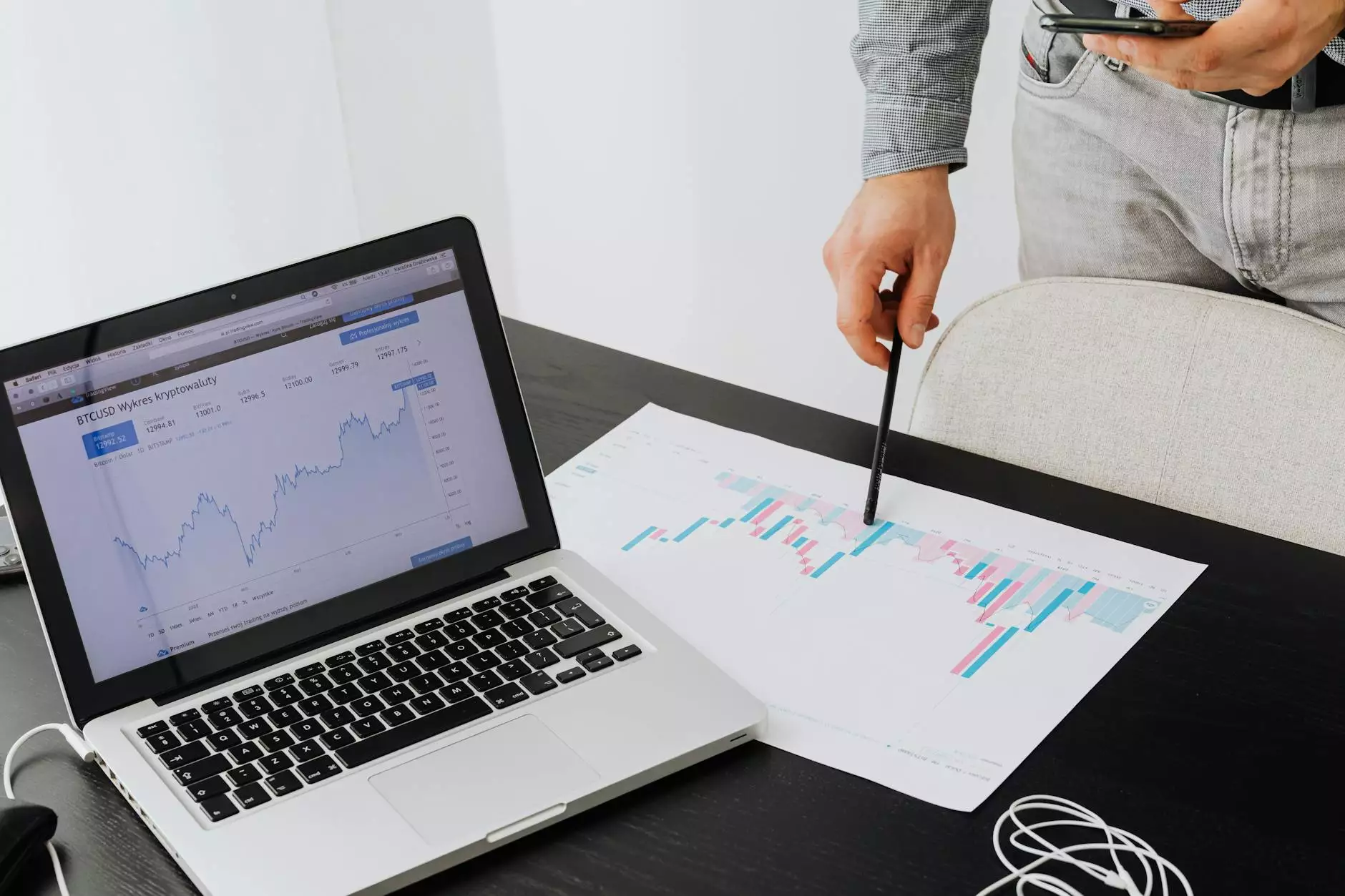
In the modern business landscape, understanding the nuances of various operational frameworks is crucial for success. One such pivotal framework is the Production Service Level Agreement (SLA). This document not only delineates the expectations between service providers and clients, but also plays a critical role in ensuring efficiency, accountability, and quality in production services.
What is a Production Service Level Agreement?
A Production SLA is a formal commitment between a service provider and a client that outlines the expected level of service in production environments. It sets clear benchmarks for what clients can expect regarding service performance, reliability, and responsiveness. This agreement is fundamental for businesses that depend on consistent output and quality, especially in fields such as:
- Art Supplies
- Product Design
- 3D Printing
The Importance of Production SLA in Business Operations
In any operational capacity, having a Production SLA is vital for several reasons:
1. Establishing Clear Expectations
The primary purpose of a Production SLA is to establish clear expectations between the involved parties. This minimizes misunderstandings and provides a benchmark against which service quality can be measured. In industries like art supplies and product design, where quality is paramount, having a precise SLA can significantly enhance client satisfaction.
2. Enhancing Service Accountability
With a Production SLA in place, service providers are held accountable for their performance. This accountability fosters a sense of responsibility, encouraging providers to meet or exceed the defined service levels. In contexts involving 3D printing, where multiple variables can affect output quality, accountability is crucial.
3. Facilitating Better Resource Management
Production SLAs allow for better resource management by defining specific metrics that serve as a guide for resource allocation. By having clear benchmarks, businesses can ensure that their resources are optimally utilized, leading to enhanced productivity and efficiency.
4. Continuous Improvement
Production SLAs can drive continuous improvement within organizations. As businesses assess their performance against agreed service levels, they can identify areas for enhancement. This is particularly important in the fast-paced environments of product design and 3D printing, where the landscape is constantly evolving.
Key Components of a Production SLA
To be effective, a Production SLA should encompass several critical components:
1. Service Description
Clearly outline what services are being provided, including any specific products, in this context, related to art supplies, product design, and 3D printing.
2. Performance Metrics
Define performance metrics that can be quantitatively measured. This includes aspects such as:
- Response time
- Resolution time
- Uptime percentage
- Service quality levels
3. Client Responsibilities
Clarify the responsibilities of the clients as well. This section prevents unfulfilled expectations by highlighting what is required on the client's part for the successful delivery of services.
4. Reporting and Review Processes
Include provisions for regular reporting and review processes. These discussions allow for evaluations of performance and necessary adjustments to the SLA itself, maintaining its relevance in a changing business environment.
Implementing Effective Production SLAs
To implement effective Production SLAs, businesses should follow some best practices:
1. Engage Stakeholders Early
Involve all relevant stakeholders in the creation of the SLA. This means including representatives from the production team, management, and even clients if necessary. Their insights will ensure that the SLA is comprehensive and practical.
2. Develop Realistic and Measurable Goals
When defining performance metrics, it is crucial to set goals that are achievable yet challenging. Unrealistic targets can lead to frustration and a breakdown of trust between providers and clients.
3. Review and Revise Regularly
Establish a routine review process for the SLA. As industries evolve, so do service requirements. Regular assessments will ensure that the SLA remains applicable and effective.
Case Studies: The Impact of Production SLAs
Let’s explore some hypothetical scenarios demonstrating the positive impact of Production SLAs in different business contexts:
Case Study in Art Supplies
Consider an art supplies company that implements a Production SLA with its suppliers. By establishing clear expectations regarding the quality and delivery times of materials, the company reduces delays in production and maintains higher customer satisfaction as a result.
Case Study in Product Design
In a product design firm, a Production SLA with their prototyping service ensures rapid turnaround times. The SLA specifies performance metrics that both parties agree upon, allowing the designer to accurately meet project deadlines, ultimately leading to increased client trust and repeat business.
Case Study in 3D Printing
A 3D printing startup could utilize a Production SLA to outline the expected quality of printed prototypes. With specific metrics for accuracy and post-processing times, the startup can build a reputation for reliability, positioning itself as a leader in the fast-expanding 3D printing market.
Conclusion: The Future of Production SLAs in Business
As industries such as art supplies, product design, and 3D printing continue to evolve, the importance of a well-structured Production SLA cannot be understated. These agreements lay the foundation for successful partnerships, fostering trust, accountability, and excellence in service delivery.
By recognizing the value of Production SLAs, businesses position themselves not only to meet current demands but also to adapt to future challenges in a fast-paced marketplace. This forward-thinking approach will undoubtedly contribute to their long-term success and sustainability.