The Importance of a Prototype Mold Factory in Modern Manufacturing
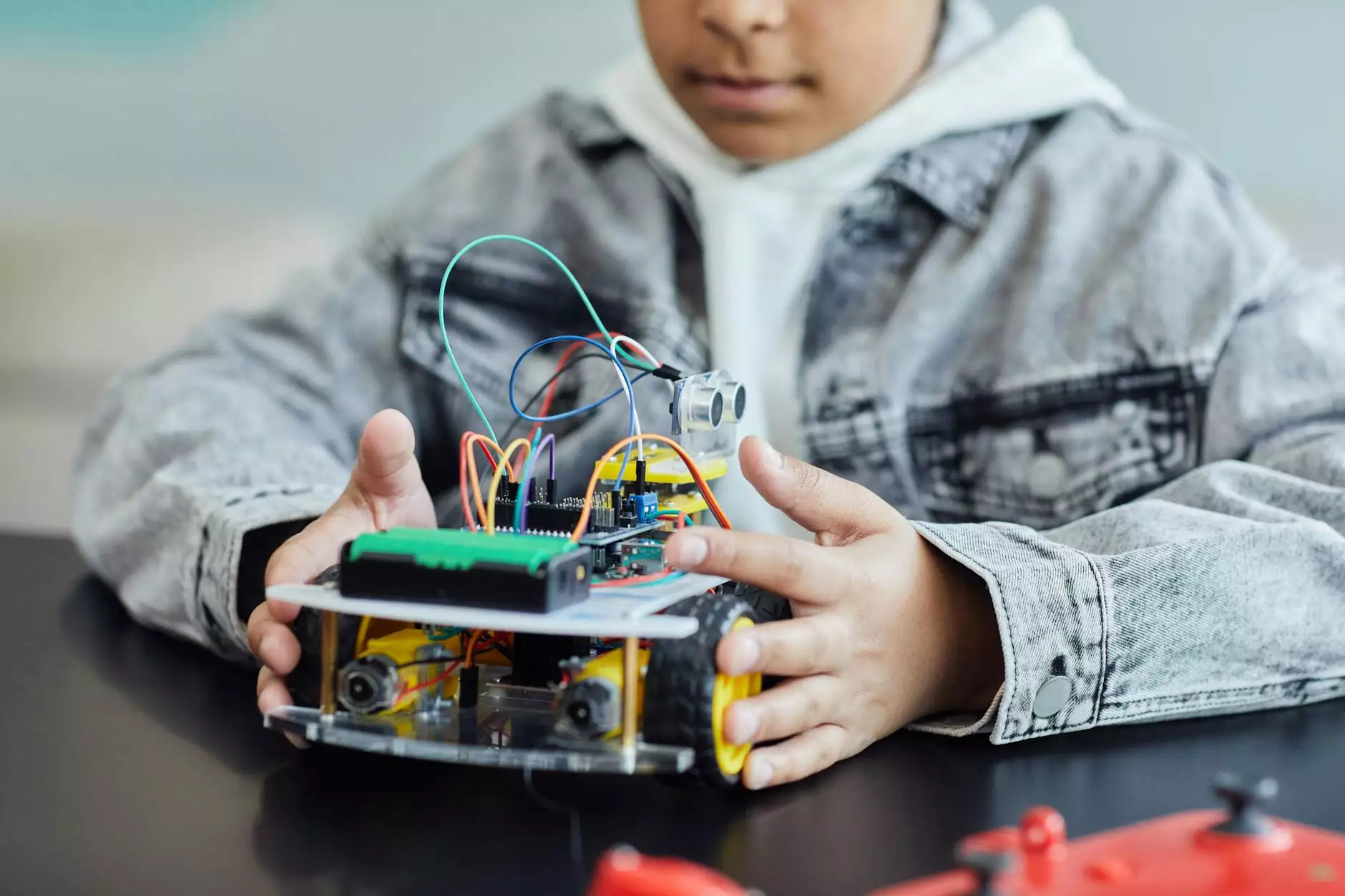
The landscape of manufacturing has evolved remarkably in recent years, and at the forefront of this transformation is the prototype mold factory. In today's competitive market, businesses are increasingly relying on advanced prototype molds to enhance their product development cycles. This article delves into the intricacies of a prototype mold factory, its contributions to the manufacturing sector, and how it positions companies for success.
Understanding Prototype Mold Factories
A prototype mold factory specializes in creating molds that enable rapid production of prototypes. These molds are crucial for testing new designs and concepts before mass production. The importance of a prototype mold factory cannot be overstated, as it helps eliminate costly errors and accelerates the time-to-market for products.
Benefits of Using a Prototype Mold Factory
Engaging with a prototype mold factory presents numerous advantages:
- Cost Efficiency: By allowing businesses to test prototypes, these factories help identify flaws early in the process, significantly reducing costs associated with large-scale production.
- Faster Time to Market: With rapid prototyping capabilities, companies can quickly iterate their designs and get their products into the hands of consumers sooner.
- Enhanced Product Quality: Prototype molds facilitate thorough testing under real-world conditions, ensuring that the final product is of the highest quality.
- Flexibility in Design: The prototyping process allows for modifications and improvements based on feedback, leading to innovative and user-centric products.
Key Processes in a Prototype Mold Factory
The operations in a prototype mold factory involve several critical processes:
1. Design and Engineering
The initial phase involves creating detailed designs using computer-aided design (CAD) software. Engineers and designers collaborate to ensure that every aspect of the mold meets the specifications required for the prototype.
2. Mold Fabrication
This phase includes the physical creation of the mold. Materials such as steel or aluminum are commonly used, chosen for their durability and ability to produce high-fidelity prototypes.
3. Testing and Evaluation
After the mold is fabricated, it is tested to evaluate its performance. This step is crucial for identifying any design flaws or potential improvements.
4. Iteration and Refinement
Based on testing outcomes, changes may be made to the mold to optimize it for production. This iterative process is paramount in achieving a perfect design.
What Makes a Great Prototype Mold Factory?
Not all prototype mold factories are created equal. Here are some features that distinguish the best in the industry:
- Advanced Technology: Utilization of state-of-the-art machinery and techniques ensures precision and efficiency in mold production.
- Skilled Workforce: Expertise in metal fabrication and molding processes is vital. A knowledgeable team can navigate complex challenges and deliver exceptional results.
- Customer-Centric Approach: A great prototype mold factory focuses on understanding the unique needs of its clients, offering tailored solutions that meet specific requirements.
- Strong Quality Control: Implementing robust quality assurance practices guarantees that every prototype meets the highest standards.
The Role of Metal Fabricators in Prototype Mold Production
Metal fabricators play a pivotal role in the operation of a prototype mold factory. Their expertise in manipulating various metals is crucial for producing high-quality molds that can withstand the rigorous demands of production. Here’s how they contribute:
Precision Cutting and Shaping
Metal fabricators employ a range of techniques such as laser cutting, CNC machining, and welding to create the intricate molds required for prototyping. Their skill ensures that every piece is cut to the exact specifications needed for perfect functionality.
Assembly Expertise
The assembly process is just as important as the initial fabrication. Metal fabricators use their experience to assemble complex mold components with precision and care, ensuring optimal performance during the prototyping phase.
Materials Knowledge
Understanding various metals and their properties is crucial. Fabricators select the most suitable materials to enhance the durability and functionality of the prototypes being developed.
Industries Benefiting from Prototype Mold Factories
A prototype mold factory serves a wide array of industries, contributing significantly to innovation and efficiency. Below are some of the key sectors that benefit:
1. Automotive Industry
The automotive industry relies heavily on rapid prototyping to develop new models and parts. Prototype molds enable manufacturers to test vehicle components extensively before committing to mass production.
2. Consumer Electronics
In the fast-paced world of consumer electronics, companies must continuously innovate. Prototype mold factories allow for quick development cycles for electronic devices, ensuring they meet market demands.
3. Medical Devices
In the medical field, safety and functionality are paramount. The ability to prototype medical devices ensures they are user-friendly and effective before entering production.
4. Aerospace
The aerospace industry needs highly specialized components designed with precision. Prototype molds enable engineers to test and refine intricate designs crucial for safety and performance.
Challenges Faced by Prototype Mold Factories
While prototype mold factories offer invaluable benefits, they also face several challenges:
1. Design Complexity
As product designs grow increasingly sophisticated, creating molds that accurately reflect these designs can be challenging. It requires advanced technology and expertise to overcome this hurdle.
2. Material Limitations
Different products require different materials, and sourcing the right materials can be difficult. Fabricators must stay informed about new materials and advancements in metalworking techniques.
3. Cost Management
The initial investment in technology and skilled labor can be substantial. Managing costs while delivering high-quality prototypes is a constant balancing act for factory operators.
Success Stories: Companies Thriving with Prototype Molds
There are numerous examples of companies that have harnessed the power of a prototype mold factory to fuel their success:
Case Study 1: Tesla
Tesla has effectively used rapid prototyping to innovate its electric vehicle designs. By leveraging prototype molds, the company has been able to bring products to market faster than traditional automotive manufacturers.
Case Study 2: Apple
Apple's commitment to sleek and innovative design is matched by its investment in rapid prototyping. By utilizing prototype mold factories, Apple consistently pushes boundaries in consumer electronics.
Case Study 3: GE Healthcare
GE Healthcare has transformed its approach to medical device development by integrating rapid prototyping techniques. This change has improved product functionality and reduced time to market.
The Future of Prototype Mold Factories
Looking ahead, the future of prototype mold factories is promising. Key trends indicate an evolution in their role:
1. Automation and AI
The integration of automation and artificial intelligence in fabrication processes is set to enhance efficiency and consistency in mold production.
2. Sustainable Practices
As sustainability becomes a priority, more prototype mold factories are adopting eco-friendly practices, from material sourcing to waste management.
3. Additive Manufacturing
3D printing technology is starting to influence prototyping processes, offering new ways to create molds that are both cost-effective and innovative.
Conclusion: Embracing the Future of Manufacturing
In conclusion, the prototype mold factory plays an instrumental role in the advancement of modern manufacturing. By embracing rapid prototyping, companies can reduce costs, enhance product quality, and get to market faster than ever before. As technology continues to evolve, so too will the capabilities of prototype mold factories, solidifying their place as essential partners in the product development landscape. For businesses looking to leverage innovative manufacturing solutions, aligning with a proficient prototype mold factory can pave the way for sustained success.