Die Casting China Supplier: The Key to Global Manufacturing Success
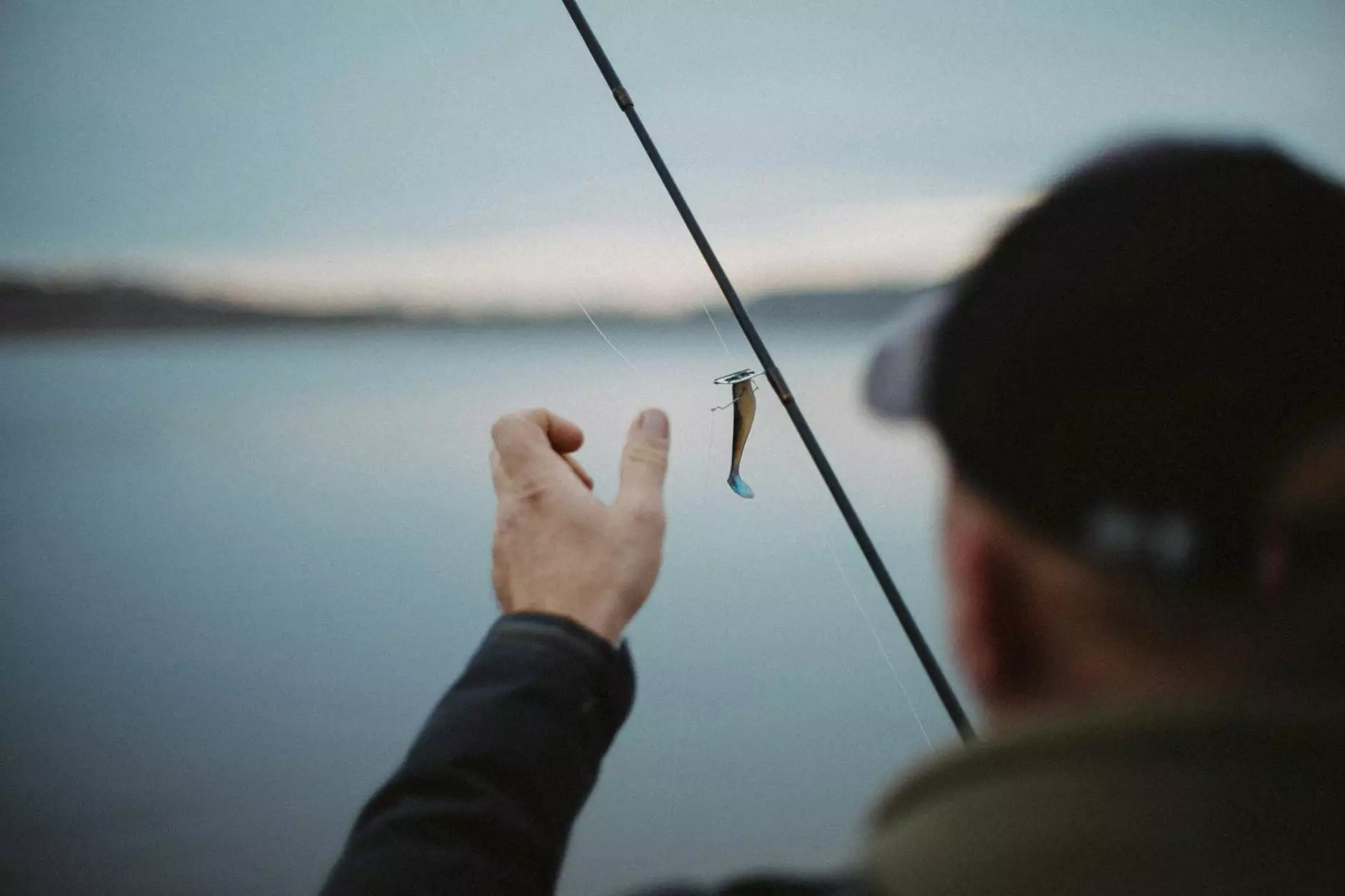
In the vast landscape of global manufacturing, one of the most critical decisions for businesses is the selection of an efficient and reliable supplier. Among the various options, a die casting China supplier stands out as a promising choice for many industries. This article delves into the several aspects of die casting in China, highlighting the advantages, process, and tips for choosing the best suppliers to maximize your manufacturing success.
The Importance of Die Casting in Manufacturing
Die casting is a manufacturing process that involves forcing molten metal into a mold cavity. It is widely celebrated for its ability to produce parts with exceptional accuracy, surface finish, and dimensional consistency. The following are some key benefits of die casting:
- High Precision: Die casting produces components with very tight tolerances, making it suitable for industries requiring high-performance parts.
- Efficiency: The rapid cycle time of die casting means that a high volume of parts can be produced in a short period, reducing production time.
- Complex Geometries: The technology enables the production of intricate designs that are difficult to achieve through other manufacturing methods.
- Material Versatility: A range of metals can be used in die casting, including zinc, aluminum, and magnesium, offering flexibility in material selection.
Why Choose a Die Casting China Supplier?
Choosing a supplier from China for your die casting needs can be a strategic decision. Here are several reasons why collaborating with a die casting China supplier can benefit your business:
1. Cost-Effectiveness
One of the most significant advantages of sourcing from China is the lower cost of manufacturing. Due to the country's advanced manufacturing capabilities and economies of scale, components produced are often more affordable than those made in other regions. Businesses can save substantially in production costs, which can be redirected to other areas like marketing or R&D.
2. Advanced Technology and Equipment
Many die casting suppliers in China leverage cutting-edge technology and high-quality equipment. This investment in technology not only improves the quality of the casting but also enhances the overall production process through automation and precision engineering.
3. Experienced Workforce
China's manufacturing sector is supported by a vast pool of skilled labor. The expertise available allows for greater innovation while ensuring that quality standards are met consistently. A die casting China supplier will likely possess years of experience in design and manufacturing, leading to better project outcomes.
4. Scalable Production
When business expansion leads to increased demand, having a supplier capable of scaling production is vital. Chinese die casting suppliers can accommodate varying order sizes, making it easier to adjust production based on the current market needs.
5. Fast Lead Times
With efficient manufacturing processes, many Chinese suppliers can offer reduced lead times, allowing businesses to respond quickly to market changes and customer demands. This agility is a competitive edge that can be transformative in industries requiring quick turnaround times.
Understanding the Die Casting Process
To fully appreciate the advantages of working with a die casting China supplier, it is crucial to understand the die casting process itself. The following steps outline the typical die casting process:
Step 1: Mold Design
The first step involves designing a mold that reflects the desired component's specifications. This design phase is critical as it determines the shape, size, and finish of the final product.
Step 2: Metal Melting
The chosen metal (commonly zinc, aluminum, or magnesium) is then heated in a furnace to its melting point. The molten metal must be handled with care to prevent any contamination that could affect the final product.
Step 3: Injection
Once the metal is melted, it is injected under high pressure into the prepared mold. This high-pressure injection is important for achieving the precision and detail of the component.
Step 4: Cooling and Solidifying
After injection, the molten metal cools and solidifies within the mold. This phase usually takes a matter of seconds and is crucial for maintaining the dimensional integrity of the part.
Step 5: Ejection
Once the metal has solidified, the mold opens, and the component is ejected. At this stage, additional finishing processes may be required, such as surface treatment or machining, to ensure the component meets quality and design specifications.
Step 6: Quality Control
Finally, the parts undergo rigorous testing and quality control checks to ensure that they meet the required standards before being shipped to the client. This stage is vital for maintaining the high-quality reputation of suppliers.
How to Select the Right Die Casting Supplier in China
Finding the right die casting China supplier can be a daunting task, especially with many options available. Here are some tips to help you choose the best supplier for your needs:
1. Research and Reviews
Start by conducting thorough research. Look for reviews and testimonials from other customers. Online platforms and forums can provide valuable insights into the supplier's reliability and quality of work.
2. Certifications and Standards
Check if the supplier possesses relevant certifications such as ISO 9001. Certifications are an indication of a company’s commitment to maintaining high-quality standards and efficient operational processes.
3. Production Capabilities
Assess the supplier’s production capabilities. Ensure they have the right equipment, technology, and workforce to meet your specific requirements in terms of quality and quantity.
4. Communication
Effective communication is essential. Choose a supplier that maintains open lines of communication and can quickly address any concerns or questions you may have throughout the process.
5. Sample Quality
Request samples of previous work. Reviewing the quality of their finished products can provide insight into what you can expect when fulfilling your order.
Common Applications of Die Casting
Die casting is widely employed across various industries. Here are some common applications:
- Automotive: Parts such as engine blocks, transmission housings, and other critical components are commonly made using die casting.
- Consumer Electronics: Die casting is used for creating housings for devices such as smartphones, laptops, and other electronic gadgets.
- Industrial Machinery: Many components in industrial machinery, including connectors and pump housings, are produced through die casting.
- Aerospace: Lightweight metal components required for aircraft structures and interiors are often manufactured using this method.
Conclusion: The Advantages of Partnering with a Die Casting China Supplier
In conclusion, working with a die casting China supplier offers a multitude of benefits that can streamline your manufacturing process and enhance product quality. With cost-effective solutions, advanced technology, and an experienced workforce, Chinese die casting suppliers are poised to support businesses in achieving their manufacturing goals.
By understanding the die casting process, recognizing the various applications, and selecting the right supplier, businesses can leverage die casting solutions to gain a competitive edge in the global market. Whether you are in the automotive sector, consumer electronics, or industrial manufacturing, collaborating with a reliable die casting supplier in China can lead to transformative results in your production strategy.