Precision Plastic Injection Molding: Transforming Manufacturing Processes
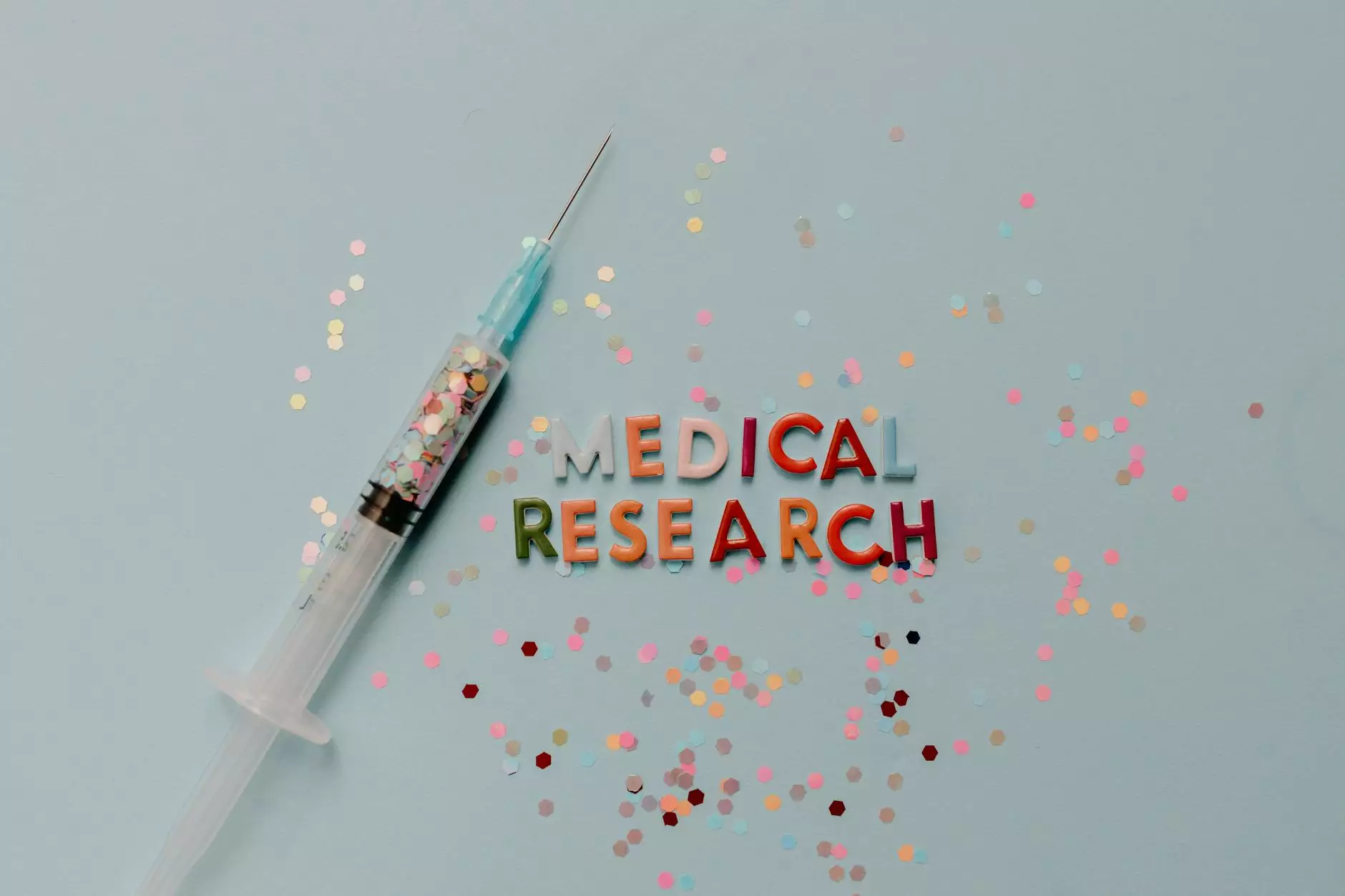
The world of manufacturing is constantly evolving, and one of the most significant advancements in this field is precision plastic injection molding. This innovative process has revolutionized the way various industries produce parts and products, enabling businesses to achieve high levels of accuracy, efficiency, and customization. In this article, we will explore the intricate details of precision plastic injection molding, its benefits, applications, and how it can lead to superior results for manufacturers, particularly in the domain of metal fabricators.
What is Precision Plastic Injection Molding?
Precision plastic injection molding is a manufacturing process that involves injecting molten plastic material into a mold cavity to create specific shapes and components. This technique is known for its exceptional accuracy and repeatability, making it ideal for producing intricate parts that require tight tolerances.
How the Process Works
- Material Selection: The process begins with choosing the appropriate thermoplastic material that meets the specific requirements of the product.
- Mold Design: Engineers design a mold that will accommodate the desired shape and features of the plastic component. This mold is typically made from steel or aluminum and must be designed to withstand high pressures and temperatures.
- Injection: The selected plastic is heated until it melts and is injected into the mold under high pressure. This ensures that the material fills every detail of the mold cavity.
- Cooling: After the mold is filled, it is cooled, allowing the plastic to solidify and take the shape of the mold.
- Demolding: Once cooled, the mold is opened and the finished product is ejected. Additional processes, like trimming and finishing, may follow to ensure product quality.
Benefits of Precision Plastic Injection Molding
Companies that utilize precision plastic injection molding enjoy a plethora of advantages, which include:
- High Precision: Achieving tolerances of ±0.001 inches is common, making it perfect for industries requiring stringent specifications.
- Cost-Effectiveness: Although initial mold creation can be expensive, the cost per part decreases significantly with higher production volumes.
- Fast Production Rates: Injection molding allows for rapid production cycles, greatly increasing output and efficiency.
- Material Versatility: A wide variety of plastics can be used, including engineered resins that enhance properties like strength and heat resistance.
- Reduced Waste: The injection molding process generates minimal waste compared to other manufacturing methods, offering an environmentally friendly advantage.
Applications of Precision Plastic Injection Molding
The applications of precision plastic injection molding span several industries, including:
1. Automotive Industry
Automotive manufacturers rely heavily on injection molding for producing interior components, dashboards, and exterior trim pieces. This method ensures that parts adhere to safety standards while also enhancing aesthetic appeal.
2. Medical Device Manufacturing
In the medical field, precision is paramount. Injection molding allows for the creation of complex components such as syringes, casings for diagnostic equipment, and intricate assemblies used in surgical devices. The cleanroom processes often associated with medical manufacturing can also be integrated into injection molding operations.
3. Consumer Electronics
Products such as mobile phone casings, connectors, and complex internal mechanisms benefit from the precision and adaptability of injection molding. With the rapid pace of technological advancement, manufacturers can customize products quickly to meet changing consumer demands.
4. Household Products
Everyday items like containers, toys, and kitchenware are increasingly produced using precision plastic injection molding. This method not only promotes higher production rates but also allows for the creation of ergonomic designs that enhance user experience.
Challenges in Precision Plastic Injection Molding
While precision plastic injection molding offers numerous advantages, it also poses some challenges that manufacturers must navigate:
- High Initial Costs: The manufacturing of molds can be a significant investment, impacting cash flow, particularly for small to medium enterprises.
- Complex Design Requirements: The design of molds must be executed with precision from the start. Errors can lead to extensive rework and increased costs.
- Material Limitations: Not all plastics are suitable for injection molding; understanding material compatibility is key to ensuring the quality of the final product.
Innovation in Precision Plastic Injection Molding
The industry is witnessing continuous innovation aimed at improving the precision plastic injection molding process. Advancements in technology such as:
- 3D Printing: Rapid prototyping through 3D printing has made it easier for engineers to create and test mold designs before committing to the final product.
- Smart Manufacturing: The integration of IoT and AI in the production process optimizes efficiency, monitors production in real-time, and reduces downtime.
- Eco-Friendly Practices: Increasing emphasis on sustainability is leading manufacturers to explore recycled materials and greener production processes.
The Role of DeepMould in Precision Plastic Injection Molding
At DeepMould, we specialize in delivering high-quality precision plastic injection molding services tailored specifically to the needs of our clients in the metal fabricators sector. Our commitment to excellence in manufacturing processes, combined with our state-of-the-art technology, allows us to produce complex components with unmatched consistency and quality.
Why Choose DeepMould?
- Expertise: With years of experience, our team is well-versed in the intricacies of injection molding, ensuring that customer needs are met.
- Advanced Technology: We utilize the latest machinery and software to enhance productivity while minimizing errors.
- Customized Solutions: Every project is different; we provide tailored solutions to meet specific design and production requirements.
- Quality Assurance: Our rigorous quality control processes guarantee that every product meets the highest industry standards.
Conclusion
In conclusion, precision plastic injection molding stands at the forefront of modern manufacturing, offering unmatched precision and efficiency across various industries. With continuous advancements and innovations, it remains a vital component of the manufacturing landscape. Companies like DeepMould are leading the charge by providing high-quality solutions that meet the ever-changing demands of the marketplace. Embracing this technology not only enhances manufacturing capabilities but also positions businesses for long-term success in a competitive world.
Get Started with Precision Plastic Injection Molding Today
If you’re ready to elevate your manufacturing process and explore the advantages of precision plastic injection molding, contact us at DeepMould.net. Our expert team is here to guide you through every step, ensuring your vision becomes a reality.